Florida’s unique climate poses significant challenges for concrete structures. Common issues include cracking due to environmental stressors, spalling from corrosion and moisture intrusion, discoloration, scaling, and efflorescence. Coastal areas face additional salt damage risks, while high humidity fosters mold growth. Thermal expansion and contraction, along with reinforcement corrosion, further compromise structural integrity. Addressing these problems involves proper mix design, sealant application, drainage improvements, and specialized repair techniques. Regular maintenance, including cleaning and inspection, is crucial. Preventive measures such as corrosion-resistant materials and thermal-resistant concrete mixes can mitigate long-term damage. Understanding these issues and their solutions is key to maintaining durable concrete structures in Florida’s demanding environment.
Cracking and Its Causes
Cracking stands out as one of the most prevalent concrete issues in Florida, often stemming from a variety of causes. These cracks can range from superficial hairline fissures to deep structural fractures, each requiring different approaches to concrete maintenance.
The primary factors contributing to concrete cracking in Florida include environmental stressors, such as extreme temperature fluctuations, high humidity, and exposure to saltwater.
Shrinkage cracking occurs as concrete cures and loses moisture, a process exacerbated by Florida’s hot climate. Thermal expansion and contraction due to daily temperature variations can lead to thermal cracking.
Additionally, settlement cracks may form when the underlying soil shifts or settles unevenly. Overloading, improper mixing ratios, or inadequate reinforcement can result in structural cracks that compromise the concrete’s integrity.
Florida’s proximity to saltwater bodies introduces chloride-induced corrosion, where salt penetrates the concrete and corrodes reinforcing steel, causing expansive cracking.
Freeze-thaw cycles, though less common in Florida, can still occur in northern regions, leading to surface scaling and cracking. Identifying the specific cause of cracking is crucial for implementing effective repair strategies and preventing further deterioration.
Spalling: Surface Deterioration
Concrete spalling, a common issue in Florida’s harsh climate, manifests as surface deterioration characterized by flaking, chipping, or scaling of the concrete.
Understanding the causes of spalling, which include corrosion of reinforcing steel, freeze-thaw cycles, and chemical exposure, is crucial for effective prevention and treatment.
Accurate identification of spalling damage and knowledge of appropriate repair techniques are essential for maintaining the structural integrity and longevity of concrete structures in Florida’s challenging environment.
Causes of Concrete Spalling
Surface deterioration, known as spalling, poses a significant threat to concrete structures in Florida. This phenomenon occurs when the concrete’s surface begins to flake, chip, or crumble, exposing the underlying reinforcing steel. Environmental factors play a crucial role in the development of spalling, with Florida’s humid climate and coastal proximity exacerbating the issue.
The primary causes of concrete spalling include:
- Moisture intrusion and subsequent freeze-thaw cycles
- Corrosion of reinforcing steel due to chloride ion penetration
- Alkali-silica reaction (ASR) between cement and certain aggregates
Moisture intrusion is particularly problematic in Florida’s climate, as it facilitates the corrosion of reinforcing steel. When steel corrodes, it expands, creating internal pressure that leads to cracking and spalling.
Additionally, the state’s proximity to saltwater sources accelerates chloride ion penetration, further promoting steel corrosion.
The alkali-silica reaction occurs when certain silica-rich aggregates react with alkalis in cement, forming a gel that expands in the presence of moisture. This expansion causes internal stresses, leading to cracking and spalling.
Understanding these causes is essential for implementing effective preventive measures and developing appropriate repair strategies for concrete structures in Florida’s challenging environment.
Identifying Spalling Damage
Having understood the causes of concrete spalling, it becomes imperative to recognize its manifestations in structures. Identifying spalling damage early is crucial for effective spalling prevention and maintaining structural integrity.
Visual inspection is the primary method for detecting spalling, with key indicators including:
- Surface flaking or peeling
- Exposed reinforcement bars
- Rust stains or discoloration
- Cracking patterns, particularly in a circular or map-like formation
- Hollow sounds when tapping the concrete surface
Advanced detection techniques may involve ultrasonic testing, impact-echo methods, or ground-penetrating radar to assess internal damage. These non-destructive tests can reveal hidden deterioration before it manifests on the surface.
Monitoring for spalling should be conducted regularly, with increased frequency in areas prone to moisture exposure or chemical attack.
Implementing a comprehensive surface protection strategy can mitigate spalling risks. This may include applying sealants, waterproofing membranes, or corrosion inhibitors to vulnerable areas.
Early identification and prompt intervention are essential for preserving concrete structures and minimizing repair costs, underlining the importance of vigilant inspection protocols in Florida’s challenging environmental conditions.
Spalling Repair Techniques
Three primary approaches are employed in repairing concrete spalling: patching, resurfacing, and replacement. Patching involves filling small, localized areas of damage with a compatible repair mortar. Resurfacing is utilized for more extensive surface deterioration, applying a thin layer of concrete or specialized overlay material. Complete replacement is necessary when structural integrity is compromised.
Spalling prevention is crucial for long-term concrete durability. Surface treatments can significantly extend the life of concrete structures by:
- Applying penetrating sealers to reduce moisture intrusion
- Installing waterproof membranes on horizontal surfaces
- Utilizing corrosion inhibitors to protect reinforcing steel
The repair process begins with thorough surface preparation, including removal of loose material and cleaning. For patching and resurfacing, proper bonding agents are applied to ensure adhesion.
Specialized repair materials, often polymer-modified, are selected based on the extent of damage and environmental conditions. Curing is critical to achieve optimal strength and durability.
In severe cases, cathodic protection systems may be installed to mitigate ongoing corrosion. Regular inspections and maintenance, including reapplication of surface treatments, are essential for preventing future spalling and ensuring the longevity of concrete structures in Florida’s challenging coastal environment.
Discoloration and Staining
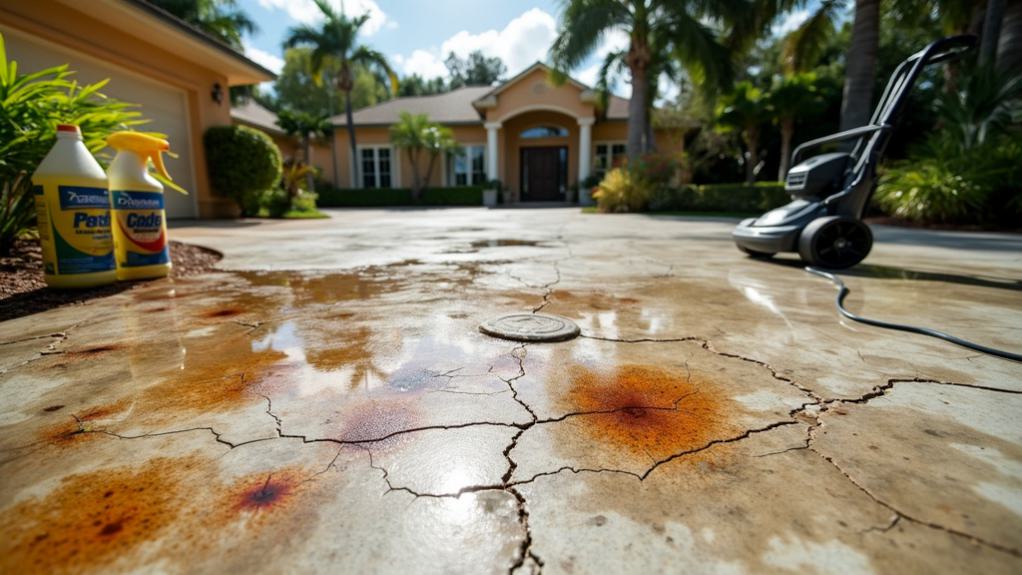
Concrete discoloration and staining in Florida often result from various environmental and chemical factors.
Common causes include moisture penetration, efflorescence, organic growth, and iron oxidation from reinforcing steel.
Effective stain removal techniques depend on the specific type of discoloration and may involve pressure washing, chemical treatments, or mechanical abrasion methods.
Causes of Concrete Discoloration
Frequently, Florida homeowners encounter the vexing issue of concrete discoloration, which can significantly impact the aesthetic appeal of their properties. This phenomenon stems from various factors, both intrinsic and extrinsic to the concrete itself. Environmental factors play a crucial role in initiating and exacerbating color variations across concrete surfaces.
The primary causes of concrete discoloration in Florida include:
- Inconsistent mixing ratios of cement, water, and aggregates
- Uneven curing conditions due to fluctuating humidity and temperature
- Chemical reactions between concrete components and environmental contaminants
Efflorescence, a common manifestation of discoloration, occurs when soluble salts within the concrete migrate to the surface, leaving a white, powdery residue. Additionally, the presence of organic matter, such as leaves or algae, can impart localized staining.
Iron-containing aggregates may oxidize, resulting in rust-colored patches. The use of different cement batches or inconsistent water-to-cement ratios during placement can lead to noticeable color discrepancies.
Furthermore, the application of deicing salts, prevalent in some Florida regions, can induce surface scaling and subsequent discoloration. Understanding these underlying causes is essential for implementing effective preventive measures and remediation strategies.
Stain Removal Techniques
Restoration of discolored or stained concrete surfaces in Florida requires a methodical approach tailored to the specific type of discoloration or staining present. The first step in the process is to identify the nature of the stain, whether it’s organic, inorganic, or caused by environmental factors.
For light staining, pressure washing can be an effective initial treatment, utilizing high-pressure water to dislodge surface contaminants.
For more stubborn stains, chemical cleaners may be necessary. Acid-based cleaners are effective for removing inorganic stains like rust or mineral deposits, while alkaline solutions work well for organic stains such as oil or grease. It’s crucial to select the appropriate cleaner to avoid exacerbating the discoloration or damaging the concrete surface.
After applying the chemical cleaner, thorough rinsing is essential to neutralize the surface and prevent further chemical reactions.
In cases of deep-set stains, mechanical abrasion techniques may be required, such as diamond grinding or shot blasting. These methods remove a thin layer of the concrete surface, effectively eliminating embedded stains.
Following stain removal, applying a protective sealer can help prevent future discoloration and maintain the restored appearance of the concrete.
Scaling: Flaking and Peeling
Surface deterioration known as scaling occurs when the top layer of concrete begins to flake or peel away, exposing the aggregate beneath. This issue is particularly prevalent in Florida due to the state’s humid climate and exposure to saltwater in coastal areas. Scaling compromises both the aesthetic appeal and structural integrity of concrete surfaces, necessitating prompt attention and remediation.
Common causes of concrete scaling include:
- Freeze-thaw cycles, although less frequent in Florida
- Poor finishing techniques during installation
- Excessive water in the concrete mix
Prevention strategies and maintenance tips are crucial for mitigating scaling issues. Proper concrete mix design, adequate curing time, and the application of high-quality sealants can significantly reduce the risk of scaling.
Regular inspections and timely repairs of minor damage can prevent scaling from progressing. In areas prone to saltwater exposure, implementing protective measures such as cathodic protection systems may be necessary.
When scaling occurs, treatment options vary based on severity. Minor scaling may be addressed through surface grinding and resurfacing, while more extensive damage may require complete replacement of the affected area.
Consulting with a concrete specialist is advisable to determine the most appropriate remediation approach.
Efflorescence: White Powder Deposits

Efflorescence, a common issue in Florida’s concrete structures, manifests as white, powdery deposits on the surface of concrete and masonry materials. This phenomenon occurs when water-soluble salts within the concrete or surrounding soil migrate to the surface through capillary action and evaporate, leaving behind crystalline deposits. The high humidity and frequent rainfall in Florida exacerbate this problem, making it particularly prevalent in the region.
The primary causes of efflorescence include excessive moisture, high salt content in the concrete mix or adjacent soil, and inadequate drainage. To address this issue, it is crucial to identify and eliminate the source of moisture.
Preventing efflorescence formation involves implementing proper drainage systems, applying water-resistant sealants, and using low-alkali cement in concrete mixtures. Additionally, ensuring proper curing techniques and maintaining appropriate water-to-cement ratios during construction can significantly reduce the likelihood of efflorescence occurrence.
In existing structures, efflorescence can be removed through mechanical means such as wire brushing or pressure washing, followed by the application of a penetrating sealer to prevent future salt migration. Regular maintenance and prompt addressing of water infiltration issues are essential for long-term prevention of efflorescence in Florida’s concrete structures.
Sinking and Settlement Issues
Concrete sinking and settlement issues in Florida often stem from the state’s unique geological conditions, including unstable soil and high water tables.
Common causes include soil erosion, poor compaction during construction, and voids created by underground water movement.
Addressing these problems typically involves foundation repair techniques such as slab jacking, pier installation, or chemical grouting to stabilize and potentially lift the affected concrete structures.
Causes of Concrete Settling
Several factors contribute to concrete settling in Florida, a common issue that affects driveways, sidewalks, and building foundations. The state’s unique geological and climatic conditions exacerbate this problem, leading to significant structural challenges for property owners.
Soil compaction plays a crucial role in concrete settling. When the underlying soil is not adequately compacted before construction, it can gradually compress under the weight of the concrete, causing uneven settling. This issue is particularly prevalent in areas with sandy or organic soils, which are common throughout Florida.
Water drainage problems also contribute significantly to concrete settling. Poor drainage can lead to:
- Soil erosion beneath the concrete
- Weakening of the soil structure
- Creation of voids that cause instability
The high water table and frequent heavy rainfall in Florida further compound these drainage issues. Additionally, the state’s susceptibility to sinkholes can cause sudden and severe settling of concrete structures. These geological formations occur when underground limestone dissolves, creating cavities that can collapse under the weight of surface structures.
To mitigate concrete settling, proper site preparation, including thorough soil compaction and implementation of effective drainage systems, is essential.
Regular maintenance and prompt addressing of any signs of settling can help prevent more severe structural problems in the future.
Fixing Sinking Foundations
Addressing sinking foundations in Florida requires specialized techniques and expertise due to the state’s unique geological challenges. Foundation repair methods must account for the region’s high water table, sandy soils, and limestone bedrock. Common approaches include underpinning with helical or push piers, which transfer the structure’s weight to more stable soil layers or bedrock.
Soil stabilization techniques are often employed in conjunction with underpinning to address the underlying causes of settlement. These may involve chemical grouting, which strengthens loose soils by injecting a binding agent, or compaction grouting, which densifies the soil by injecting a low-mobility grout under high pressure.
In cases where voids are present beneath the foundation, polyurethane foam injection can be used to fill these spaces and provide additional support.
For less severe cases of settlement, mudjacking or slabjacking may be sufficient. This process involves pumping a cement-based slurry beneath the affected area to lift and level the foundation.
Regardless of the chosen method, proper drainage improvements and moisture control measures are essential to prevent future settlement issues in Florida’s challenging environment.
Salt Damage in Coastal Areas

Frequently, coastal areas in Florida face significant challenges related to salt damage in concrete structures. Saltwater intrusion poses a severe threat to the integrity of concrete, leading to accelerated deterioration and structural instability. The high concentration of chloride ions in seawater penetrates concrete pores, initiating corrosion of reinforcing steel and causing expansion, cracking, and spalling.
To mitigate salt damage and implement effective corrosion prevention strategies, coastal property owners and builders should consider the following measures:
- Utilize high-performance concrete mixes with low water-to-cement ratios
- Apply protective coatings or sealants to concrete surfaces
- Implement cathodic protection systems for reinforcing steel
The selection of appropriate materials and construction techniques is crucial in combating salt damage. Incorporating supplementary cementitious materials, such as fly ash or silica fume, can enhance concrete density and reduce permeability.
Additionally, employing stainless steel or fiber-reinforced polymer (FRP) reinforcement can significantly improve corrosion resistance in coastal environments. Regular inspections and maintenance, including the application of penetrating sealers and crack repairs, are essential for prolonging the service life of concrete structures exposed to saltwater intrusion.
Mold and Mildew Growth
In Florida’s humid climate, mold and mildew growth presents a persistent challenge for concrete structures. The high moisture content in the air, combined with warm temperatures, creates an ideal environment for these microorganisms to thrive on concrete surfaces.
Mold and mildew not only compromise the aesthetic appeal of concrete but can also lead to structural degradation over time.
To combat this issue, implementing effective preventive measures is crucial. Moisture control plays a pivotal role in mitigating mold and mildew growth. Proper drainage systems, waterproofing treatments, and adequate ventilation can significantly reduce moisture accumulation on concrete surfaces.
Additionally, applying specialized sealants and coatings can create a barrier that inhibits microbial growth.
Regular maintenance and cleaning routines are essential for long-term mold and mildew prevention. Utilizing appropriate cleaning agents and techniques can effectively remove existing growth and deter future colonization.
In severe cases, professional remediation may be necessary to address extensive mold infestations and restore the integrity of the concrete structure.
Thermal Expansion and Contraction

Florida’s extreme temperature fluctuations pose a significant challenge for concrete structures due to thermal expansion and contraction. As temperatures rise, concrete expands, and when temperatures fall, it contracts. This cyclical process can lead to stress within the material, potentially causing cracks, spalling, and structural instability over time.
The issue is particularly pronounced in Florida due to its subtropical climate, which experiences both intense heat and occasional cold snaps.
To mitigate the effects of thermal expansion and contraction, engineers and builders must consider several factors:
- Proper joint placement and design to accommodate movement
- Selection of appropriate concrete mix designs with thermal resistance properties
- Implementation of effective thermal insulation techniques
Addressing thermal expansion and contraction requires a comprehensive approach. This includes careful material selection, precise engineering calculations, and meticulous construction practices.
Designers must account for the coefficient of thermal expansion of concrete and incorporate expansion joints at strategic locations. Additionally, the use of specialized admixtures and reinforcement can enhance the concrete’s ability to withstand temperature-induced stresses.
Regular inspections and maintenance are crucial to identify and address any developing issues promptly, ensuring the longevity and structural integrity of concrete structures in Florida’s challenging climate.
Reinforcement Corrosion
Reinforcement corrosion presents a significant threat to concrete structures in Florida’s coastal environments. The high humidity, salt-laden air, and frequent exposure to seawater accelerate the degradation of steel reinforcement within concrete structures. This corrosion process leads to the expansion of steel, causing internal stresses that result in cracking, spalling, and eventual structural failure.
Corrosion prevention strategies are crucial for maintaining the integrity of concrete structures in Florida. Material selection plays a vital role in mitigating reinforcement corrosion. Utilizing corrosion-resistant reinforcement materials, such as stainless steel or fiber-reinforced polymer (FRP) bars, can significantly extend the lifespan of concrete structures.
Additionally, implementing protective measures like cathodic protection systems or applying corrosion inhibitors to the concrete mix can further enhance resistance to reinforcement corrosion.
Regular inspections and maintenance are essential for early detection and intervention. Non-destructive testing methods, such as half-cell potential measurements and ground-penetrating radar, can help identify areas of active corrosion before visible damage occurs.
Prompt repair of cracks and spalls, along with the application of sealants or coatings, can prevent further ingress of corrosive agents and protect the reinforcement from deterioration.
Last Words
Addressing concrete issues in Florida requires a comprehensive understanding of the region’s unique environmental challenges. Proper maintenance, timely repairs, and preventive measures are crucial for extending concrete lifespan and structural integrity. Implementing water-resistant sealants, corrosion-resistant reinforcement, and climate-appropriate mix designs can mitigate many common problems. Regular inspections and professional assessments are essential for early detection and intervention. By employing these strategies, property owners and engineers can effectively manage and minimize concrete deterioration in Florida’s demanding climate. Call You Concrete Contractor in Broward County to help You!