Concrete sealing is essential for protecting investments in Florida's challenging climate. High humidity, intense UV exposure, and frequent rainfall can lead to moisture accumulation, surface degradation, and structural damage. Quality sealants create protective barriers against these environmental factors, extending concrete lifespan and maintaining aesthetic appeal. Proper sealing enhances resistance to staining, weathering, and chemical exposure while reducing maintenance costs. Various sealant types, including penetrating and film-forming options, offer different levels of protection and durability. Regular application and maintenance are crucial for optimal performance. Understanding the specific needs of your concrete surfaces and Florida's unique environmental challenges is key to selecting the most effective sealing solution.
Understanding Florida's Climate Challenges

Florida's unique climate presents three primary challenges for concrete surfaces: high humidity, intense UV exposure, and frequent rainfall. These environmental factors can significantly impact the longevity and appearance of concrete structures, necessitating proper protection through sealing.
High humidity levels in Florida contribute to moisture accumulation on concrete surfaces, potentially leading to mold growth, efflorescence, and accelerated deterioration.
Humidity effects can also cause concrete to expand and contract, resulting in micro-cracks that compromise structural integrity over time.
UV exposure is another critical concern for concrete in Florida. Intense sunlight can cause discoloration, fading, and surface degradation.
UV rays break down the chemical bonds in concrete, leading to a chalky appearance and reduced durability. This process is particularly pronounced in areas with minimal shade or protection from direct sunlight.
Frequent rainfall exacerbates these issues by increasing moisture penetration and promoting the growth of algae and other organic matter on concrete surfaces.
The combination of high humidity, UV exposure, and regular precipitation creates a challenging environment for maintaining concrete structures, underscoring the importance of proper sealing techniques in Florida's climate.
Benefits of Concrete Sealing
Concrete sealing offers significant advantages for structures in Florida's challenging climate.
The application of a high-quality sealant extends the lifespan of concrete surfaces by creating a protective barrier against moisture intrusion and chemical degradation.
This barrier also enhances the concrete's resistance to staining from various sources and provides improved weathering performance against Florida's intense sun, frequent rain, and occasional salt exposure.
Extended Lifespan
A significant benefit of concrete sealing is the substantial extension of the material's lifespan. By applying a high-quality sealant to concrete surfaces, property owners can effectively enhance the durability of their investment, protecting it from various environmental factors that contribute to deterioration.
The sealing process creates a protective barrier that prevents moisture penetration, a primary cause of concrete degradation in Florida's humid climate. This barrier mitigates the risk of water-related damage, including freeze-thaw cycles, which can lead to cracking and spalling.
Additionally, sealed concrete exhibits increased resistance to chemical exposure, UV radiation, and abrasion, further contributing to its longevity.
Investment protection is a key aspect of concrete sealing. By extending the lifespan of concrete surfaces, property owners can defer costly repairs or replacements, ultimately saving money in the long term.
The sealant also maintains the aesthetic appeal of the concrete, preserving its original appearance and reducing the need for frequent cleaning or resurfacing.
Regular reapplication of sealant, typically every 3-5 years depending on usage and exposure, ensures continued protection and maximizes the concrete's lifespan, making it a cost-effective solution for maintaining concrete structures in Florida's challenging climate.
Stain and Weather Resistance
One of the primary advantages of concrete sealing is its ability to enhance stain and weather resistance. In Florida's challenging climate, unsealed concrete is vulnerable to various staining agents, including oil, grease, and organic materials. Sealers create a protective barrier that prevents these substances from penetrating the concrete surface, making cleanup easier and maintaining the aesthetic appeal of the substrate.
Weather resistance is particularly crucial in Florida's humid, subtropical environment. Concrete sealers shield against moisture intrusion, which can lead to efflorescence, spalling, and freeze-thaw damage in cooler regions. Additionally, they offer protection from UV rays, which can cause color fading and surface degradation over time.
Many sealers also provide color enhancement, intensifying the natural hues of the concrete or amplifying the vibrancy of stained surfaces. This feature is especially beneficial for decorative concrete applications.
Furthermore, certain sealers can improve slip resistance, an important safety consideration for pool decks, patios, and other outdoor surfaces exposed to frequent moisture.
Types of Concrete Sealers
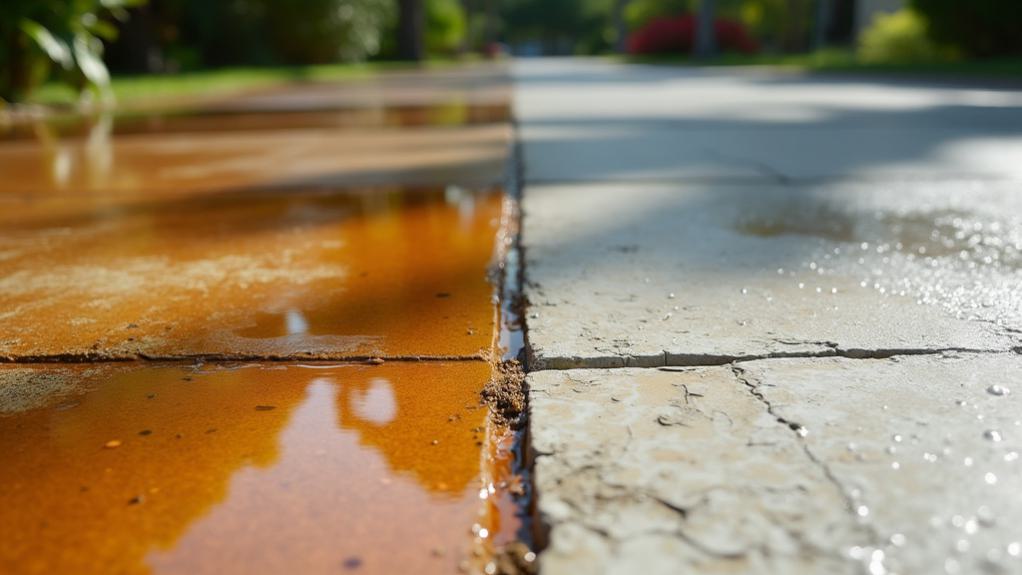
Concrete sealers are broadly categorized into penetrating and film-forming types, each offering distinct protective properties.
The composition of these sealers varies between water-based and solvent-based formulations, influencing their application methods and environmental impact.
Among the most common varieties are acrylic, epoxy, and polyurethane sealers, each with specific characteristics suited to different concrete sealing requirements in Florida's climate.
Penetrating Vs. Film-Forming Sealers
Choosing the right sealer for concrete surfaces in Florida involves understanding the two main categories: penetrating sealers and film-forming sealers.
Penetrating sealers, as the name suggests, penetrate the concrete surface, forming a protective barrier within the pores. These sealers offer excellent protection against water and chloride intrusion, making them ideal for Florida's humid climate and coastal areas. They do not alter the surface appearance significantly and provide long-lasting protection.
Film-forming sealers, conversely, create a protective layer on the concrete surface. They offer:
- Enhanced aesthetic appeal with glossy or matte finishes
- Improved stain resistance
- Easier maintenance and cleaning
However, film-forming sealers may be more susceptible to wear and tear, especially in high-traffic areas. They can also trap moisture, potentially leading to concrete deterioration if not properly applied or maintained.
The choice between penetrating and film-forming sealers depends on various factors, including the concrete's location, intended use, and desired appearance.
In Florida's challenging environment, penetrating sealers often provide superior long-term protection, particularly for exterior applications. Film-forming sealers may be more suitable for interior spaces or areas where aesthetics are a primary concern.
Water-Based Vs. Solvent-Based Options
When considering concrete sealers, the choice between water-based and solvent-based options is crucial for optimal performance in Florida's climate.
Water-based sealers offer several advantages, including low volatile organic compound (VOC) emissions, ease of application, and quick drying times. These sealers are environmentally friendly and safer for applicators, making them ideal for indoor use or areas with limited ventilation. Additionally, water-based sealers allow moisture vapor transmission, reducing the risk of trapped moisture beneath the surface.
Solvent-based sealers, while traditionally known for their durability and penetration depth, come with notable drawbacks in Florida's humid environment. These sealers emit strong odors and high VOCs, requiring proper ventilation during application. They are also flammable, posing safety risks during storage and use. Furthermore, solvent-based sealers can trap moisture within the concrete, potentially leading to surface damage and reduced longevity.
In Florida's climate, water-based sealers generally outperform their solvent-based counterparts due to their moisture-permeable nature and resistance to UV degradation.
However, the specific project requirements, concrete type, and exposure conditions should always be considered when selecting between water-based and solvent-based options for optimal concrete protection and longevity.
Acrylic, Epoxy, Polyurethane Varieties
Beyond the water-based and solvent-based categorization, concrete sealers are further classified into specific types based on their chemical composition and performance characteristics. In Florida's diverse climate, three primary varieties stand out: acrylic, epoxy, and polyurethane sealers.
Acrylic sealers offer several advantages:
- Quick drying time
- UV resistance
- Cost-effectiveness
These characteristics make acrylic sealers popular for both interior and exterior applications. However, they may require more frequent reapplication compared to other types.
Epoxy sealers are renowned for their durability and strength. They form a hard, chemical-resistant surface that excels in high-traffic areas and industrial settings. Epoxy sealers provide excellent protection against stains and abrasions but may yellow when exposed to prolonged UV light.
Polyurethane sealers combine durability with flexibility, making them ideal for surfaces subject to movement or temperature fluctuations. Their resistance to chemicals and abrasion rivals that of epoxy sealers, while offering superior UV stability.
Polyurethane sealers are available in both aliphatic and aromatic formulations, with aliphatic variants providing enhanced color retention and weather resistance.
Selecting the appropriate sealer type depends on specific project requirements, environmental conditions, and desired longevity of protection.
Application Process and Timing
The application process for concrete sealing in Florida demands meticulous attention to detail and precise timing.
Surface preparation is crucial, involving thorough cleaning to remove dirt, oil, and existing sealants. Power washing, followed by acid etching or grinding, may be necessary to ensure proper adhesion. The concrete must be completely dry before sealing, which typically requires 24-48 hours after cleaning.
Curing time for newly poured concrete is critical; most experts recommend waiting at least 28 days before applying sealant. This allows the concrete to fully cure and release excess moisture. In Florida's humid climate, moisture testing is essential to prevent trapping water beneath the sealant.
Application techniques vary depending on the sealant type. Rollers, sprayers, or squeegees may be used, with multiple thin coats preferred over a single thick layer.
Temperature and humidity affect drying time, which can range from 4-24 hours between coats. Full curing may take up to 72 hours, during which time the surface should be protected from moisture and foot traffic.
Proper application and timing ensure optimal sealant performance and longevity in Florida's challenging climate.
Maintenance and Reapplication
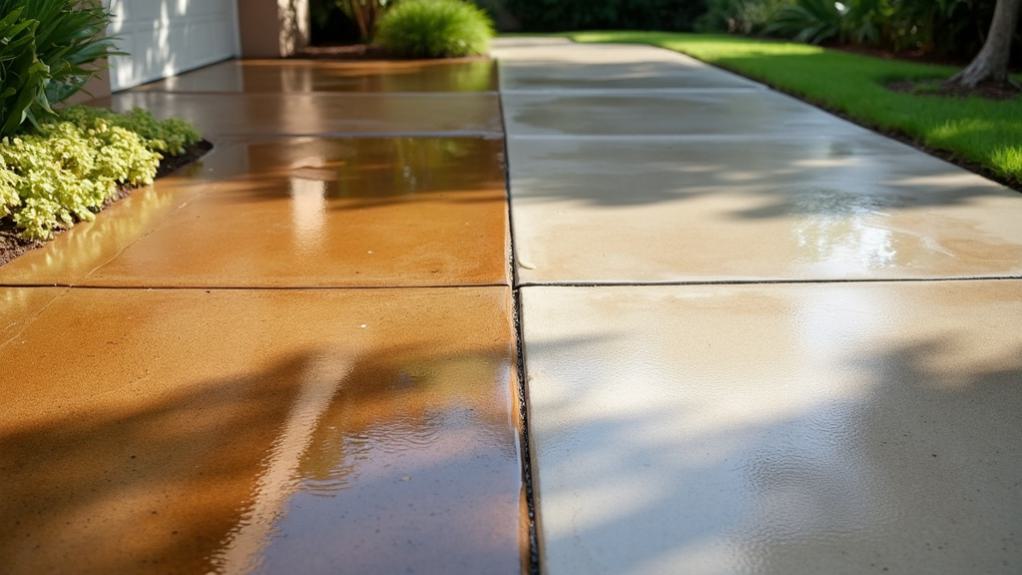
Maintaining sealed concrete surfaces in Florida's harsh climate requires regular attention and periodic reapplication to ensure optimal protection.
Regular cleaning with mild detergents and soft brushes is essential to prevent dirt buildup and maintain the sealer's effectiveness. Avoid using harsh chemicals or abrasive tools that may damage the protective layer.
Reapplication intervals depend on various factors, including sealer type, surface usage, and environmental conditions. Generally, exterior surfaces may require resealing every 2-3 years, while interior surfaces can last 3-5 years.
Signs indicating the need for reapplication include:
- Visible wear or discoloration
- Water absorption into the concrete
- Loss of shine or luster on the surface
When reapplying, proper sealer selection and surface preparation are crucial. Choose a compatible sealer that matches the original product or consult a professional for recommendations.
Thoroughly clean and inspect the surface for damages before reapplication. Remove any existing sealer if necessary, and repair cracks or imperfections.
Follow manufacturer guidelines for application techniques and curing times to ensure optimal performance and longevity of the resealed concrete surface.
Cost Considerations and ROI
When considering concrete sealing in Florida, understanding the cost implications and potential return on investment (ROI) is crucial for property owners and managers. A comprehensive cost breakdown typically includes materials, labor, and equipment expenses.
The average cost for sealing concrete in Florida ranges from $0.50 to $2.50 per square foot, depending on the type of sealant and surface conditions.
Investment benefits of concrete sealing extend beyond aesthetic improvements. Properly sealed concrete can last up to 50% longer than unsealed surfaces, reducing long-term replacement costs. Additionally, sealed concrete requires less frequent cleaning and maintenance, resulting in lower ongoing expenses.
The ROI for concrete sealing is often realized through increased property value, extended lifespan of the concrete, and reduced repair costs.
Factors affecting ROI include the quality of sealant used, proper application techniques, and adherence to maintenance schedules. High-quality sealants may have a higher upfront cost but often provide superior protection and longevity.
Property owners should consider the specific environmental challenges in Florida, such as high humidity and UV exposure, when evaluating the cost-effectiveness of concrete sealing options.
Conclusion
Concrete sealing remains an essential protective measure for Florida's harsh climate conditions. Proper sealer selection, application timing, and maintenance protocols significantly extend concrete lifespan and aesthetics. While initial costs may vary, the long-term benefits of reduced repairs, enhanced durability, and improved property value justify the investment. Regular professional assessment and reapplication ensure optimal performance. Ultimately, concrete sealing represents a critical strategy for preserving and maximizing returns on concrete infrastructure investments in Florida's challenging environment.